Carbon composite assembly: choose an adhesive solution
- Thorough surface preparation
- Adhesives suitable for composites
- Resistance to shocks and vibrations
- Solutions for structural bonding
Quote
Close
You request has been sent.
We promise to respond to you in detail within 24 hours.
In the meantime, feel free to browse our other products.
Bonding carbon fiber composites in industry
Introduced in the 1950s, carbon fibers stand out for their exceptional properties: lightweight, high strength, and corrosion resistance. To create a composite material, these fibers are impregnated with an organic matrix (or resin) and then shaped in a heated mold.
Carbon fiber is a material of choice in many industrial sectors:
✈️ Aerospace: Reduces structural weight to improve energy efficiency.
🚗 Automotive: Enhances performance and reduces the weight of premium vehicles.
🏆 Sports: Optimizes equipment for competition and durability.
🛡 Defense industry: Produces ultra-lightweight and high-strength components.
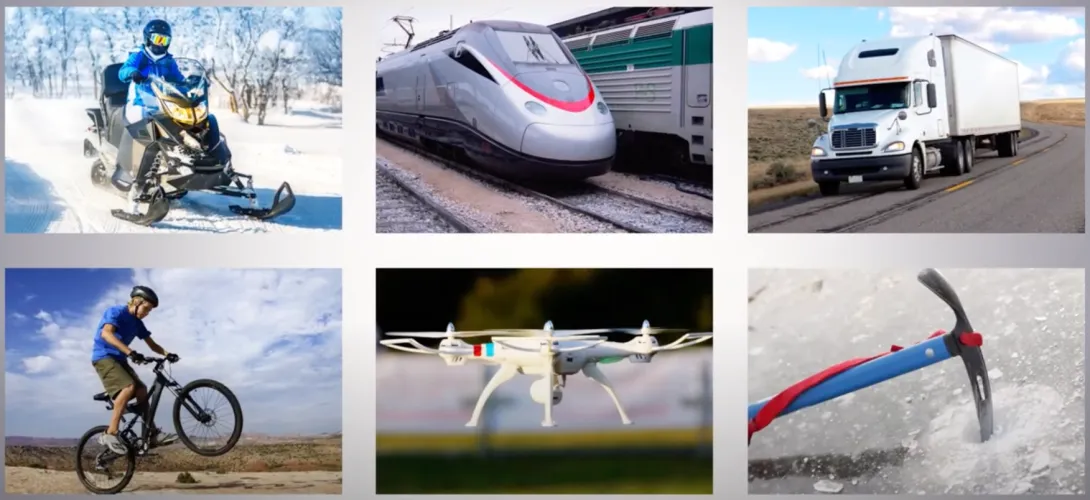
With its outstanding strength-to-weight ratio, rigidity, and durability, carbon fiber composite is essential for structural and functional components.
However, assembling carbon fiber composites presents challenges. Traditional methods like rivets, screws, or welding can weaken structures and increase component weight.
Structural adhesives offer an effective and durable alternative. Thanks to technological advances, many adhesives now make it possible to bond composites without compromising their mechanical properties.
Some suitable solutions:
Acrylic or epoxy resin construction adhesives, as well as 1-K and 2-K structural polyurethanes, for robust assemblies.
Structural adhesive films, specially designed for composites and plastics, using high-performance epoxy resins.
Low-density reinforcement sealants, ideal for strengthening honeycomb structures in automotive and aerospace construction.
Acrylic foam adhesive tapes, an effective alternative to rivets and clips for durable fixings.
Challenges of carbon composite bonding
Why avoid mechanical fasteners?
While rivets, screws, or clips provide immediate holding power, they have several disadvantages:
❌ Material weakening: Drilling creates microcracks in the composite structure.
❌ Stress concentration: Pressure at fastening points can lead to failure zones.
❌ Additional weight: Fasteners add unnecessary weight compared to adhesives.
❌ Compromised aesthetics: Visible fixings impact the final appearance.
Friction welding or heat welding may be alternatives, but these methods are energy-intensive, require costly tools, and limit part geometry.
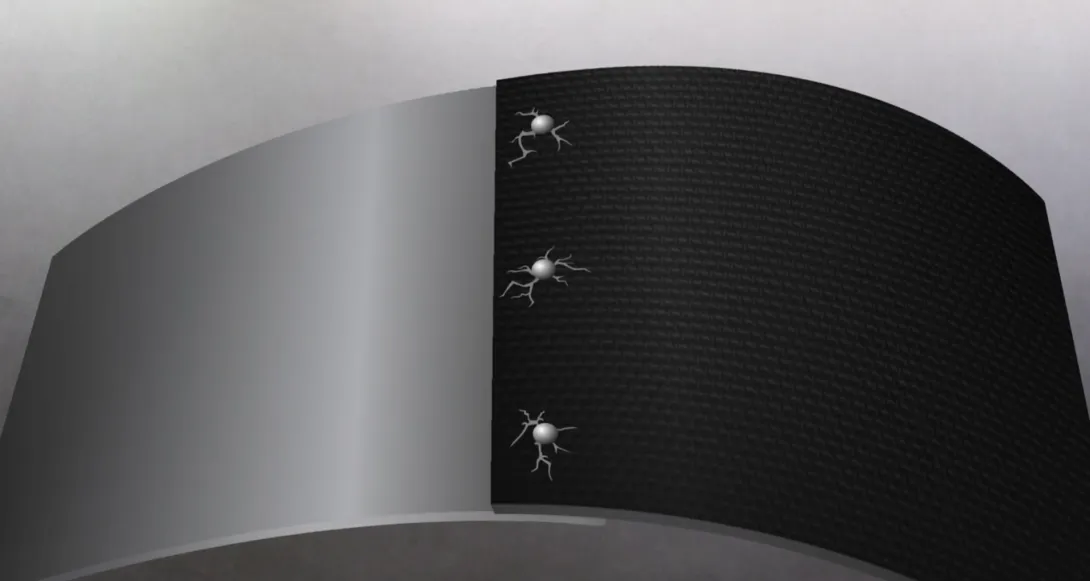
Advantages of adhesive bonding
✅ Preserves material integrity: No drilling or excessive stress on components.
✅ Even force distribution: Eliminates stress concentrations seen with rivets and welds.
✅ Lightweight assemblies: Adhesives are lighter than mechanical fasteners.
✅ Better resistance to vibration and shock: Adhesives absorb dynamic stresses.
✅ Corrosion protection: Prevents galvanic corrosion between dissimilar metals.
✅ Simplified multi-material bonding: Compatible with composites, plastics, metals, and low surface energy materials (PP, PE, TPO).
✅ Flawless aesthetics: No visible elements, no touch-ups required.
Key considerations:
The size of the parts, lamination resins, surface finish of the composites, and surface preparation are all critical when selecting the right adhesive for carbon bonding.
Applications of carbon fiber composite bonding
Thanks to its lightweight and mechanical strength, carbon fiber is used in demanding industries. Industrial bonding allows for assembly, repair, and reinforcement of components while ensuring optimal performance.
🚴 Carbon fiber bike frame repair
Bonding is essential for repairing cracked or damaged carbon bike frames, restoring rigidity and strength without adding weight.
Common in high-end cycling
Ensures performance and safety
✈️ Aerospace and marine industries
Bonding carbon composites is crucial for assembling lightweight and ultra-resistant structures, reducing fuel consumption and improving aircraft performance.
Weight optimization: Reduces component mass while maintaining strength.
Enhanced mechanical resistance: Epoxy and structural adhesives withstand mechanical stress and vibration.
Critical assembly applications: Bonding helicopter leading edges, fuselages, and support structures.
Aerospace compliance: Adhesives meet FAR 25§853 and ABD0031 standards.
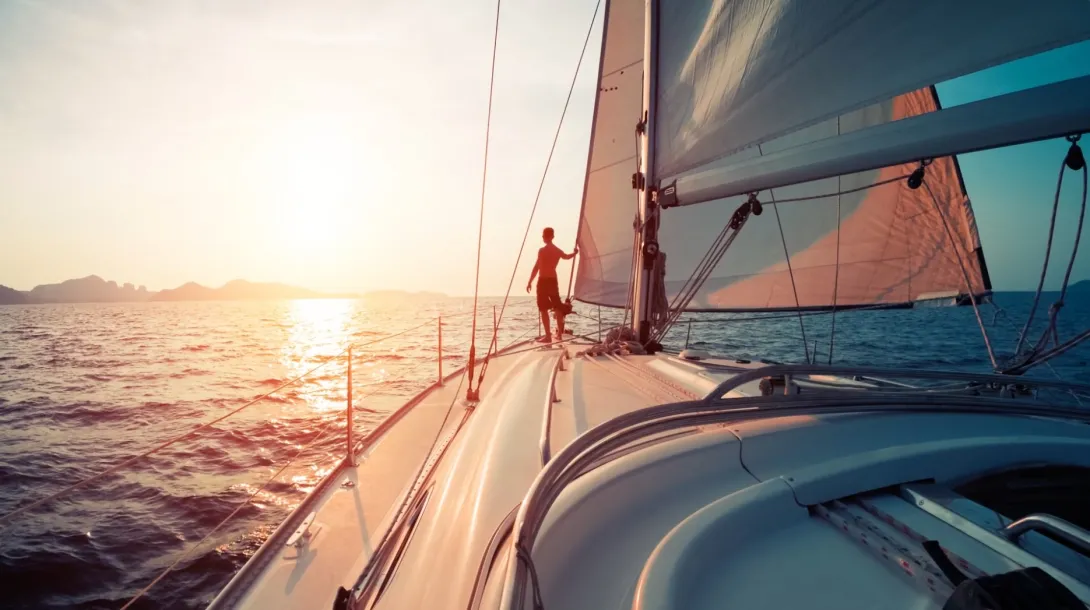
🎯 Sports equipment
Carbon bonding improves impact resistance and mechanical durability while keeping equipment light for optimal performance.
Applications include:
Windsurf boards
Fishing rods
Golf clubs
Competition bows
Baseball bats
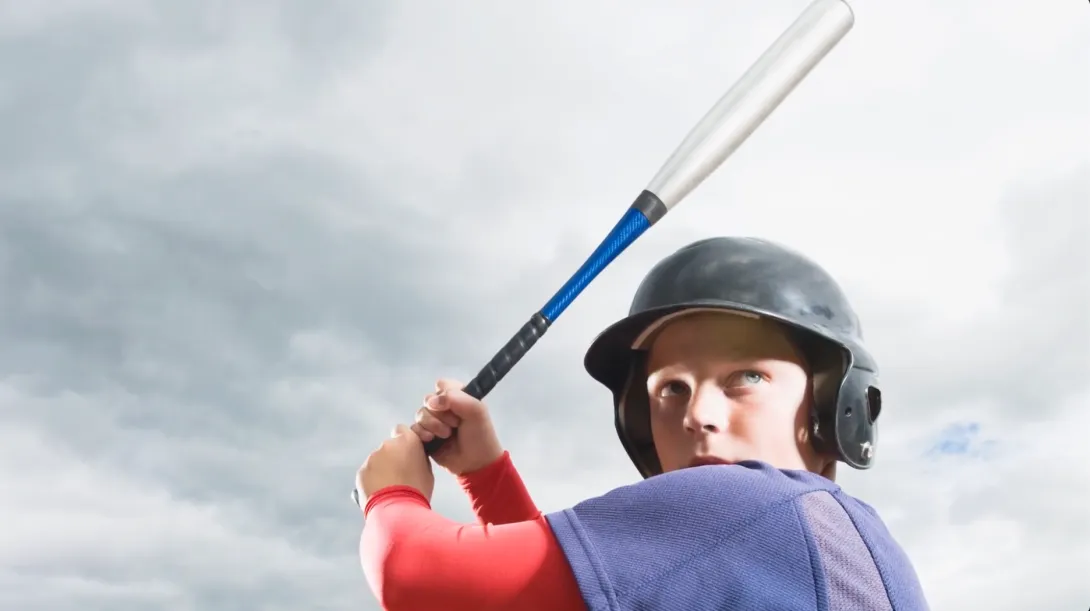
🏗️ Civil engineering and construction
Bonded carbon fiber reinforces concrete structures without adding weight—ideal for renovation and seismic upgrades.
Strengthens concrete elements
Improves mechanical resistance without extra mass
🏎️ Automotive and transportation
Bonding carbon fiber components replaces mechanical fasteners, reducing vehicle weight and improving performance and fuel efficiency.
Used in racing and premium vehicles
Improves performance and fuel economy
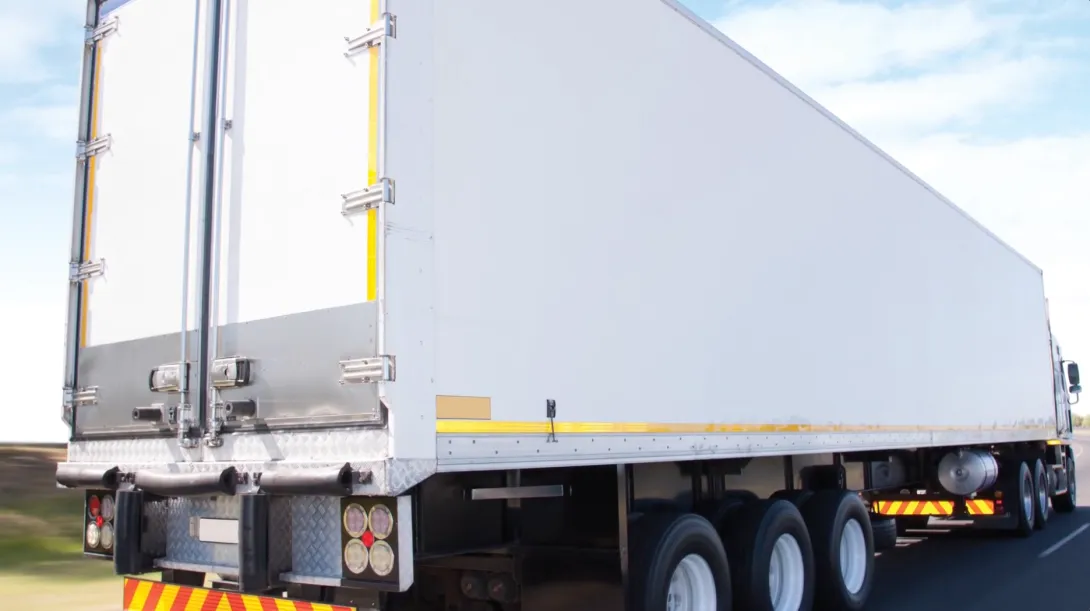
Adhesive solutions for carbon fiber composite bonding
Key factors when selecting a structural adhesive
Your assembly requirements, final application, and materials influence the optimal bonding solution. Consider these criteria to choose the right adhesive:
What materials will be bonded?
What environment (temperature, humidity, UV exposure)?
What forces will the joints endure (shear, tension, compression)?
Does it need chemical resistance (oil, fuel, acids, bases)?
Are there mechanical challenges (impact, vibration, stress)?
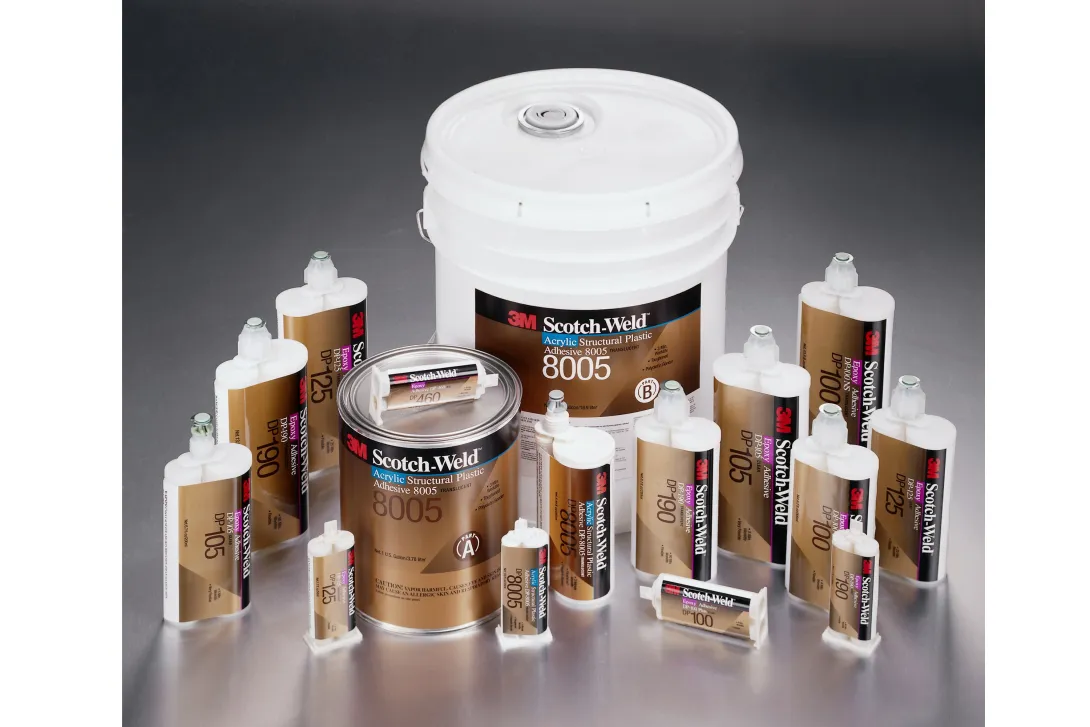
Adhesive type | Features | Examples |
---|---|---|
Epoxy | First choice for carbon bonding. High mechanical/thermal resistance. | 3M Scotch-Weld epoxy adhesives, DP100, DP110, DP190, DP410, DP420, DP490, DP760 / SikaPower 1511, 1576 |
Acrylic | Strong bonds, faster cure times, tolerant to oily or unprepared surfaces. | Loctite HY 4080 / SikaFast-555 L05 / Penloc GTI / ThreeBond TB 1530 |
Polyurethane | Absorbs shock and vibration, offers flexibility. | 3M Scotch-Weld DP620NS, DP6310NS, DP6330NS / Sika Sikaflex-552 AT |
Aerosol adhesive | Quick and uniform application, ideal for light fixings and fast processes. | 3M 71 Composite Spray Adhesive |
and 3M VHB tapes | Easy to apply, strong for non-structural bonds. | Adezif MV282, Adezif MV550, Adezif MV560, Adezif MV708, Adezif MV812, Adezif MV833, Adezif MV843 |
Transfer adhesive tape | High tack, moisture-resistant, performs on polyethylene and other low surface energy materials. | 3M 9472LE / 3M 9485PC, Adezif TF085 |
Adhesives for carbon fiber composite
Adhesives by second substrate type :
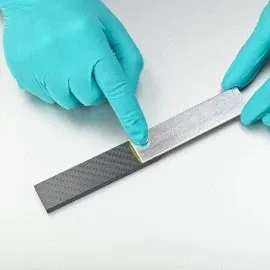
Material type | Substrate examples | Recommended adhesives |
---|---|---|
Fiber-reinforced epoxy | - Carbon fiber (CFRP) - Glass fiber | DP420NS, DP6310NS, DP760 |
Fiber-reinforced thermosets | - Polyester (FRP) - Phenolic - SMC | DP6310NS, DP8410NS, DP760 |
Thermoplastics | - Polyolefin - PET | DP8010 Blue |
Other thermoplastics | - Acrylic / PMMA - Polycarbonate (PC) - Rigid PVC / High-impact polystyrene | DP8410NS, DP6310NS |
Fiber-reinforced nylon | - Fiber-reinforced nylon | DP6310NS |
📞 Need expert advice or a quote?
Each carbon fiber bonding application has specific requirements for adhesion, mechanical strength, and durability. Adezif experts are ready to help you find the best solution for your needs.
📩 Contact us today!