Glass adhesion and assembly processes in the manufacturing industry
- Permanent, discreet, aesthetic, transparent assemblies
- How to bond glass to glass, wood, or plastic?
- Choose an adhesive solution that provides elasticity and safety
Quote
Close
You request has been sent.
We promise to respond to you in detail within 24 hours.
In the meantime, feel free to browse our other products.
Avoid glass fragility with adhesion science
Modern industry integrates glass into 85% of its innovations. Used across sectors like construction and aerospace, this material provides both elegance and functionality.
Glass boasts many strengths that make it ideal for a wide range of industrial applications: transparency, chemical resistance, hygiene, thermal performance, recyclability, and manufacturing flexibility. However, it has the reputation of being fragile and challenging to bond with other substrates.
How can you ensure a glass assembly that is both aesthetic and durable? Why choose an adhesive solution over traditional mechanical fixing methods? Special glue, adhesive tape, sealant… which is the ideal adhesive solution for your project?
Explore all our tips for achieving perfect glass assemblies.
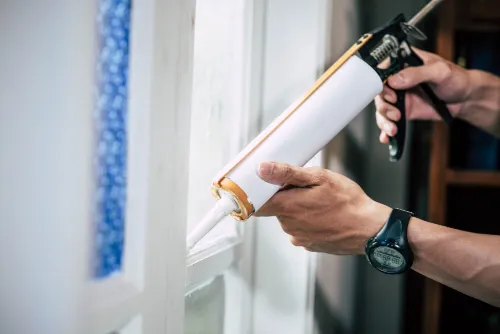
Your expectations for glass bonding:
The bonding and fixing of glass present several concerns for industrials and manufacturers:
Long-term reliability: Industrials require bonding solutions that provide durable strength, especially for glass. A failed bond could have serious consequences, from simple degradation to safety risks.
Versatility: The bonding solution must be compatible with a variety of materials, not just glass, as glass assemblies are often hybrid. Using inappropriate adhesives can also result in chemical reactions that damage the glass or other materials.
Application speed: Solutions must be easy and fast to use to maintain production speed. Some products, like glue or sealants, can be tricky to apply (handling, drying times…).
Standards compliance: Many industries have specific standards, especially in the construction sector (e.g., safety, fire resistance, environmental responsibility). Solutions that do not meet these standards can cause compliance issues.
Glass bonding in industry
Why opt for glass bonding over mechanical assembly?
Beyond the clean aesthetic, modern glass bonding techniques offer significant flexibility and durability, eliminating the need for visible, bulky fasteners.
Discretion and aesthetics: Unlike mechanical methods, bonding doesn’t introduce visible elements like screws or nails. The result is a nearly invisible assembly, perfect for applications where aesthetics are a priority.
Uniform stress distribution: Adhesives distribute forces evenly across the contact surface, reducing the risk of stress concentration, which can lead to cracks or breaks in the glass.
Compatibility with other materials: Adhesive solutions allow for the bonding of glass to many other materials, opening the door to innovative designs and hybrid applications.
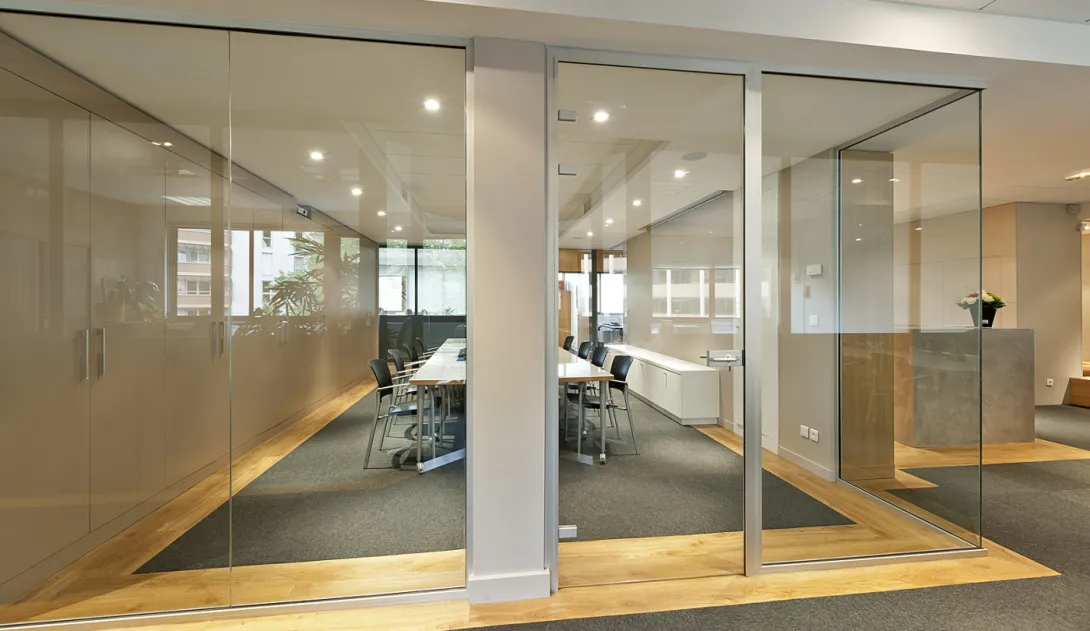
Whether it's for architectural glazing, electronic components, or designer furniture, glass is everywhere. Each of these applications requires specific and adapted bonding techniques.
Frequent applications:
- Window manufacturing:
- Double-glazed windows: structural bonding between the PVC or aluminum frame and the glass
- Bonded external glazing (VEC)
- Glass bonding in frames
- Fixing of muntin bars
- Glass partitions systems:
- Removable glass partitions
- Shower screens (joints between glass panels)
- Glass infill in a hollow profile
- Windshields:
- Moisture-resistant joints, rain sensor mounting, elastic bonding to absorb vibrations
- Moisture-resistant joints, rain sensor mounting, elastic bonding to absorb vibrations
- Furnishing and decoration:
- Edge-to-edge bonding of glass partitions
- Removable mounting of HPL panels, sandwich panels, cladding, decoration, access panels
- Mirror bonding
- Insulation bonding, spraying rock wool and glass wool laminates
- Point of sale displays (PLV), showcases
- Masking tape, surface protection
- Pads for stacking glass panels on top of each other
- Polishing operations
- Protection after glass fabrication or during transport
Important to know Due to the hydrophilic nature of glass, the adhesion of adhesive tapes is weakened by potential moisture penetration at the interface between the tape and glass. Moisture can cause bond deterioration and delamination.
The solution to counter moisture migration during your glass bonding: use a silane primer for glass, as offered by 3M. |
Main glass bonding technologies
Technology | Advantages | Disadvantages | Common Applications |
---|---|---|---|
Cyanoacrylate glues | Very fast curing, often within seconds. Versatile, easy to use. Strong adhesion on small surfaces. Ideal for precise bonding. Transparent | Poor resistance to shocks and vibrations. May leave a whitish residue around the joint (blooming). Weak resistance to water and high temperatures | Electronic components, small parts, medical applications for disposable devices, toy and model making |
Anaerobic adhesives | Cures in the absence of air. Good thermal and chemical resistance. Various viscosities for different applications. Forms a sealed joint that can prevent corrosion on metal parts | Requires primer on porous materials. Curing can be slow without an activator. Some formulas may be moisture-sensitive. Surfaces need to be well adjusted for maximum efficiency | Automotive: engine component sealing, fixing bearings, gears, and shafts in mechanical equipment, hydraulic connections, and piping |
Acrylic adhesives | Excellent adhesion on a wide variety of materials. More flexible than cyanoacrylates, better at resisting shocks and vibrations. Good aging and weather resistance | Curing can be affected by temperature and humidity. Some formulas may require curing equipment (UV light, heat). Less transparent than cyanoacrylates | Vehicle assembly: windshields or body parts, bonding composite panels in aerospace and transportation, fixing components in renewable energy sectors like solar panels |
| Transparent, excellent adhesion on many materials, chemical and thermal resistance, mechanical strength | Long drying time, poor UV resistance (yellowing, loss of flexibility). Its hardness can cause strain on glass if the part is too large | Small parts bonding onto metal, e.g., glass restoration |
| Strong, flexible, elastic assembly: resistance to thermal expansion. Versatile, resistant to diluted acids and bases, moisture, and solvents | Not transparent, lower mechanical strength than epoxies, water sensitivity, long curing time | Window bonding in transportation and construction, e.g., windshields, portholes, wood-glass glazing, insulating glass |
Silicone joints and hybrid sealants
| Cures with moisture in the air. Works with all materials. Flexible and elastic bonding. Waterproof to liquids and gases. Resistant to aging, weather, humidity, heat, and chemicals (solvents). UV-resistant (no yellowing) | Higher refractive index compared to glass: less discreet, long curing time | Applications between -40°C and +350°C depending on formulation, ideal for very humid environments or solvent exposure. Examples: aquariums, terrariums, ceramic glass plates, ovens, shower walls and handles |
| Easy and quick to assemble (no heating or complex process), clean and aesthetic bonding (sometimes transparent), instant multi-material bonding, seals and bonds at the same time, durable, vibration and shock resistant, reduces noise | Not suitable for gap filling, generally lower mechanical strength than structural glues | Suitable for large surfaces exposed to temperature variations, vibrations, or shocks. Examples: appliances, partitions, mirrors, glass doors and windows |
| Instant curing with UV exposure (speed and control), transparency, aesthetics, chemical, water, and high-temperature resistance, versatile on various types of glass (tempered, laminated, laminated) | Requires UV protective equipment, limited to thin joints | Automotive glazing (windshields, side windows, panoramic roofs), electronics (glass screens, sensors), furniture, glass panels on building façades, optical instruments, lenses |
How to choose your adhesive solution for glass?
Glass itself is not particularly difficult to bond. The challenge arises when it needs to be bonded to a different material (glass-plastic, glass-wood, glass-metal combinations). These assemblies require specialized adhesive solutions that can compensate for:
Different thermal expansion coefficients
Differences in linear expansion
Vibrations
Dynamic forces
Each project requires a tailored approach depending on the specific objective. Some examples are listed in the table below:
Desired Effects | Recommended Adhesive Solution |
---|---|
Primary load transmission and compensation for deformation differences | Flexible glue |
Load transfer on small surfaces | High-strength rigid glue |
Static transmission with elastic bearing | High-elasticity glue |
Compensation for different thermal expansions | Elastic silicone joints |
We also offer versatile glass bonding solutions, such as Sikafast 555 L05, a fast-curing structural acrylic adhesive suitable for bonding various materials (metals, plastics, glass, wood) both indoors and outdoors.
Bonding glass to glass - performance and transparency
Key considerations:
Mechanical constraints: In industrial applications, safety must not be compromised.
Durability: The bond must withstand wear, light exposure, and chemical agents.
Cleanliness: Ensure the surfaces are perfectly clean before bonding. Even a speck of dust or a fingerprint could jeopardize the bond.
Silicone sealant
Strength: Flexibility, excellent adhesion, and moisture resistance.
Applications: Used in sectors where glass-to-glass joints are exposed to the elements, such as in glass façades.
Epoxy adhesive
Strength: High mechanical resistance, transparency, durability. Maintains cohesion under stress.
Applications: Commonly used for creating glass sculptures.
UV adhesive
Strength: Transparent bonding, controlled and rapid polymerization.
Applications: Ideal for nearly invisible joints in high-end applications such as luxury goods, jewelry, pharmaceuticals, optical devices, and perfume bottles, as well as alcohol and spirits (e.g., champagne bottles), and decorative pieces.
Focus on UV adhesiveWhen it comes to glass bonding, UV adhesive is often the go-to solution. UV adhesive cures when exposed to ultraviolet light, solidifying quickly under either natural sunlight or special UV lamps.
Caution: If working with thick or tinted glass, be aware that these types of glass can filter and block some of the UV light, making the adhesive less effective. In other words, the glass may prevent the adhesive from curing to its full bonding strength. The same applies to UV-treated glass. Be sure to understand the nature of your surfaces before bonding.
Explore our full range of UV curing adhesives and UV equipment designed to ensure effective curing of these adhesives. |
Bonding glass to metal - reliability and lightness
Key considerations:
Choose an adhesive that can withstand thermal variations if the object is exposed to significant temperature changes.
Aesthetic aspects: Some adhesives may yellow or change color over time.
Two-component epoxy adhesives
Strength: Strong bond, thermal resistance, and durability.
Applications: Used for fixing decorative glass elements onto metal structures, ideal for art or decorative installations.
Structural silicones
Strength: Flexibility, weather resistance, and long service life.
Applications: Commonly used for assembling glass panels onto metal frames, especially in architectural structures.
Anaerobic adhesives
Strength: High temperature resistance and corrosion protection.
Applications: Suitable for electronic device assemblies where glass and metal components are combined.
Bonding glass to plastic - functionality and aesthetics
Key considerations:
Differentiate between plastic types.
Consider potential deformations of the plastic.
Ensure chemical compatibility between the adhesive and the plastic.
Cyanoacrylate glue
Strength: Ultra-fast drying, versatile. Strong and quick adhesion to a wide variety of plastics.
Applications: Ideal for mass production, such as assembling electrical components, where instant bonding is required.
Adapted epoxy adhesives
Strength: Versatile adhesion, water resistance.
Applications: Used for bonding glass to plastic frames in windows or photo frames.
UV adhesives (see previous section)
Strength: Rapid curing, excellent adhesion to many plastics.
Applications: Commonly used in the manufacture of light fixtures, combining glass and plastic for a transparent finish.
Bonding glass to wood - façade construction
Key considerations:
- Consider the specific characteristics of wood, such as knots or irregularities.
- Factor in humidity and wood expansion.
- Aim for a harmonious aesthetic between the wood and the adhesive.
Polyurethane adhesives
- Strength: Water resistance, flexibility, reliable adhesion.
- Applications: Used in furniture manufacturing that combines glass and wood, requiring both strong and flexible adhesion.
Specialized silicones
- Strength: Flexibility, aesthetic adaptability.
- Applications: Ideal for creating mixed art installations for indoor settings.
Did you know?
Thanks to recent advances, wood-glass composite façades (HGV) are now possible. These elements are produced by bonding wood slats to insulating glass panels in an industrial setting using high-tech silicone. This silicone ensures an even distribution of loads while effectively balancing tensions.
Once produced, installing the prefabricated façade elements is simple—just screw them into place! |
Window manufacturing: consider adhesive tapes!
Window design professionals seek slim profiles for window and frame designs to create modern and elegant façades. The challenge is balancing aesthetics, strength, and ease of installation. Compared to traditional fixings, adhesive tapes have emerged as an innovative, efficient, and faster alternative in recent years.
Key considerations
Glass weight: Choosing an inappropriate adhesive tape could lead to catastrophic failure.
Environment: Adhesive tapes exposed to outdoor conditions like rain and sun may lose their adhesive properties. Always check compatibility with outdoor environments.
Solutions must meet the strictest building standards and withstand the test of time and environmental conditions.
Why choose glass bonding with adhesive tapes?
Increased transparency: With reduced frame widths, the glass is highlighted, offering maximum transparency. Ideal for glass panels used in exhibitions, stands, or architectural installations requiring invisible fixing.
Design freedom: Adhesive tapes allow for greater design flexibility, opening the door to innovative creations.
Production simplification: Components bonded with adhesive tape are ready for transport and installation right after manufacturing, reducing delays.
Efficiency and speed: Bonding with adhesive tapes is simpler and faster than conventional methods. No need to worry about drying times, pot life, or re-application as with silicone adhesives.
High weight support capacity: The uniform stress distribution across the glass with adhesive tape minimizes the risk of breakage.
Thermal performance optimization: By avoiding frame stiffening, better Uf values can be achieved.
Improved break-in resistance: Bonding with adhesive tapes reinforces glass resistance against break-in attempts.
Viscoelastic foams: a revolution in glazing
Double-sided viscoelastic acrylic foams (like 3M VHB) are specifically designed for glass bonding. Featuring a high-performance closed-cell acrylic adhesive, these tapes offer high viscoelasticity and strong adhesive capabilities, ensuring a durable and secure bond between glass and substrates:
Modified acrylic adhesive: Provides strong cohesion, allowing for long-term bonding between various substrates, including glass, metals, and some plastics.
Thermal resistance: Operating temperature range of -40°C to +160°C, ideal for environments with significant temperature fluctuations.
UV stability: The tape formulation is optimized to resist UV degradation, ensuring the bond’s durability in outdoor conditions.
Load performance: Dissipates dynamic loads, offering high resistance to shocks and vibrations—essential for glazing applications subject to mechanical stress.
Aesthetic and finish: Offers a clean and visible-fixing-free bond, preserving the design’s integrity by eliminating traditional fixings like screws or rivets.
Ease of application: Simplified installation process, without the need for complex surface preparation or drying time, as required by traditional adhesives.
Our main adhesive tapes for windows/glazing:
Polyethylene (PE) foams:
ADEZIF MO891: Black foam for bonding on plastic profiles, ideal for fixing glazing to a frame, such as behind a corner. Compatible with glass and powder-coated surfaces.
Transparent viscoelastic foams (3M VHB type):
ADEZIF MV550 (0.5 mm thick), MV560 (1 mm), and MV580 (2 mm) for transparent applications. Ideal for edge-to-edge glass bonding, such as joints in glass roofs. These are our reference products.
ADEZIF MV708: Black foam where transparency is not required (e.g., fixing glass in window or conservatory frames with powder-coated surfaces).
ADEZIF MV504: Repositionable viscoelastic foam. Common applications: installing insect screens or blinds on glazing. This product is also often used in point of sale displays (PLV).
Fixing a mirror without drilling the wall
For a small to medium-sized lightweight mirror, double-sided adhesive tape is ideal. This solution is compatible with a variety of surfaces such as plaster, PVC, wood, and glass. Adhesive tape can also be used to reinforce traditional mechanical fixings.
For heavier mirrors, it's recommended to use a specific mirror adhesive, such as Sikaflex 545 from Sika, which offers very high initial tack.
This type of adhesive is suitable for both indoor and outdoor applications and shows strong resistance to moisture. These adhesives are also designed not to damage the mirror surface.
Keep in mind that full polymerization of the adhesive typically occurs within 24 hours.
Glass surface protection
Protective adhesive films for glass are generally made from plastic polymers and are designed to adhere firmly to the glass surface.
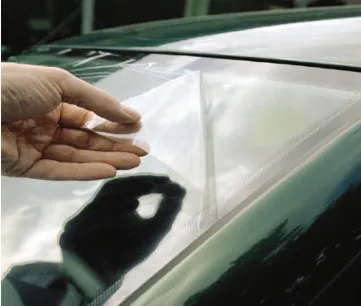
Key considerations:
When selecting a protective adhesive film, it’s essential to determine the primary need for protection (anti-scratch, security, UV resistance, etc.). The installation should be carried out meticulously to ensure perfect adhesion and avoid bubbles or irregularities so that the adhesive retains 100% of its protective properties.
Types of protective adhesive films for glass:
Anti-scratch films: These are physical protective films, primarily used to protect surfaces from everyday wear and tear. They effectively shield glass from scratches, abrasions, dust, and other physical damage, thus prolonging the lifespan of the surface.
Examples of products:
ADEZIF PV800: Electrostatic protection film without adhesive
ADEZIF PE350: Temporary adhesive protection film for glass
UV protection films: These films protect against ultraviolet rays, shielding materials behind the glass from harmful sun exposure (e.g., preventing the fading of materials behind windows).
Example:TESA 4848: Temporary protection for smooth outdoor surfaces
Heat-reflective films: These special adhesive films reflect heat, contributing to better thermal regulation of buildings and resulting in energy savings.
Security films: These films reinforce glass against impacts and prevent fragments from dispersing, reducing injury risks. Some films are specifically designed to offer increased resistance against break-in attempts.
Decorative films: While protecting glass surfaces (anti-scratch properties), these films can provide specific patterns or tints for aesthetic purposes.
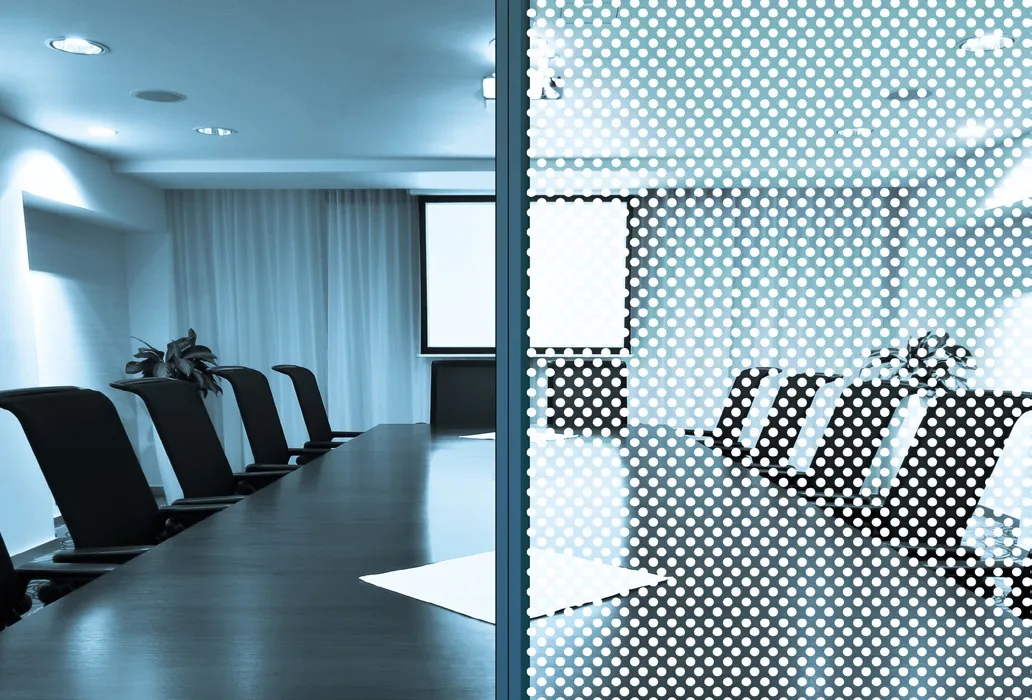
Did you know?
Some of our clients use single-sided PVC adhesive tapes to protect their glass surfaces, even though these products were not initially designed for this purpose.
Examples:
|
Have a project in mind?
Trust Adezif's technical experts to understand your challenges and provide you with high-quality, custom adhesive solutions. Contact us to discuss your needs!