Adhesive gasketing solutions for industrial flanges and joint faces
- Total leak-proof sealing
- Chemical and temperature resistance
- Replaces traditional gaskets
- Easy and quick to apply
Quote
Close
You request has been sent.
We promise to respond to you in detail within 24 hours.
In the meantime, feel free to browse our other products.
Master adhesive gasketing for rigid and flexible joint faces
Even the slightest failure on a flat gasketing joint can cause critical leaks, lead to industrial contamination, and compromise the safety of your equipment.
The result: reduced efficiency, unplanned downtime, and rising maintenance costs.
Ensuring reliable and durable gasketing on your rigid or flexible joint faces is essential to maintain the performance and continuity of your industrial operations.
Why choose an adhesive gasketing solution?
Our adhesive gasketing solutions provide key benefits:
➡️ Eliminate re-tightening operations
➡️ Prevent corrosion risks on joint faces
➡️ Reduce productivity losses related to sealing issues
Choosing an adhesive gasketing solution ensures a reliable, easy-to-apply, and long-lasting barrier to secure your equipment.
The 5 main causes of traditional gasket failures
👉 The 5 main causes of traditional gasket failures
❌ Compression set (creep or relaxation)
Traditional gaskets lose thickness over time, leading to leaks and requiring frequent re-tightening.
❌ Surface irregularities
Incomplete contact between the gasket and the joint face creates leak paths.
❌ Gasket displacement
Insufficient compression under high internal pressure can lead to gasket movement and sealing failure.
❌ Joint face deformation
Differences in thermal expansion coefficients between materials cause warping, resulting in leaks.
❌ Gasket extrusion
Under mechanical stress, traditional gaskets can extrude, reducing sealing effectiveness.
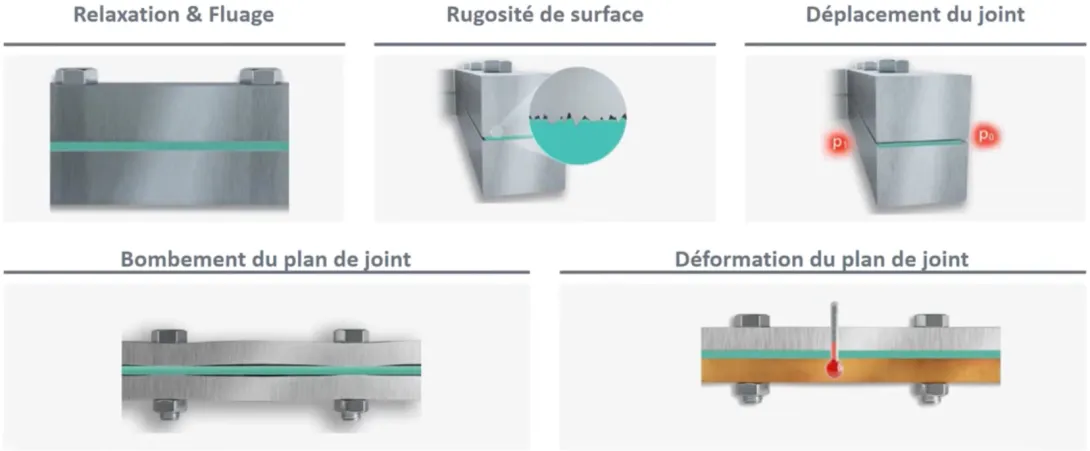
👉 Advantages of liquid gasketing solutions
✅ Fills micro-gaps and surface irregularities
✅ Eliminates seepage risks
✅ Resists vibrations and mechanical shocks
✅ Reduces inventory and maintenance costs
✅ Improves equipment safety and reliability
How to choose your adhesive flat sealing solution
Ask yourself these 5 questions to make the right choice:
Is my joint face rigid or flexible?
Is the gap less than or greater than 0.25 mm?
Are the parts made of metal, plastic, or composite?
Are they exposed to specific fluids (oil, solvents, glycol)?
Do I need a health and safety compliant product (without hazard pictograms)?
👉 Our ADEZIF technical experts are available to recommend the right adhesive gasketing solution for your industrial needs.
Which product for your application?
The choice of flat gasketing product directly depends on the type of joint face and the mechanical and environmental constraints of the application.
👉 Rigid joint faces
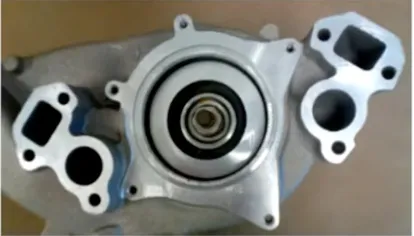
Machined surfaces
Gap ≤ 0.25 mm
Metal-to-metal rigid assemblies
Common applications:
Pump housings
Industrial gearboxes
Compressors
Combustion engines
Hydraulic blocks
Constraints:
High pressures
Resistance to oils and solvents
Requirement for perfect metal-to-metal contact
Examples of recommended products:
Loctite 518, Loctite 574, Loctite 510, Loctite 5188, Loctite 515, Loctite 5203, Loctite 5205, Loctite 5208, Loctite 5800, Born2Bond GA-18, Born2Bond GA-WL Flex, Born2Bond GA-WL Instant, Born2Bond GA-74, Born2Bond GA-10, Cyberbond 7518, Cyberbond TT69
👉 Flexible joint faces
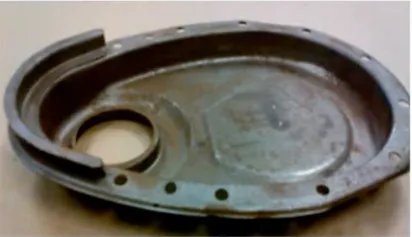
At least one non-machined surface
Gap > 0.25 mm, up to 1 mm
Assemblies subject to thermal expansion or vibrations
Common applications:
Timing chain covers
Gearbox lids
Plastic housings and covers
Metal or plastic protective covers
Constraints:
Flexibility to absorb movement
Adhesion on machined or non-machined surfaces
Compatibility with plastics and composites
Examples of recommended products:
Loctite SI 5970, Loctite SI 5926, Loctite SI 5900, Loctite SI 5910, Loctite SI 5920, Loctite SI 5980
Gasket selection based on gap size
👉 Gap ≤ 0.25 mm (anaerobic gasketing)
Product | Application | |
---|---|---|
LOCTITE 574 Born2Bond GA-74 | ![]() | Rigid metal parts such as cast iron components and pump housings. |
LOCTITE 518 Born2Bond GA-18 Cyberbond 7518 | ![]() | Rigid joint faces in iron, steel and aluminum. |
LOCTITE 510 Born2Bond GA-10 | ![]() | Rigid joint faces requiring high thermal and chemical resistance. |
LOCTITE 5188 | ![]() | All types of rigid metal joint faces, particularly aluminum. Ideal for demanding applications. Excellent chemical resistance, very flexible. superior adhesion. Tolerates slight oil contamination on joint faces. |
LOCTITE 5800 | ![]() | Health and safety version of Loctite 518. No hazard pictograms, no warnings, no safety advice. White safety data sheet. Excellent chemical and thermal resistance once cured |
👉 Greater than 0.25 mm (silicone gasketing, plastics, metals):
Product | Application | |
---|---|---|
LOCTITE SI 5926 | ![]() | Flexible silicone sealant for metal, plastic, and painted surfaces. Resists vibrations, thermal expansion, and mechanical stress. |
LOCTITE SI 5699 | ![]() | Suitable for various joint faces, including stamped sheet metal covers. Offers resistance to water/glycol. NSF P1 compliant. Skin forms in 10 minutes. |
LOCTITE SI 5970 | ![]() | Replacement for traditional paper or cork gaskets on stamped covers. Recommended for high vibration and deformation. Skin forms in 25 minutes. |
Surface preparation
Components must be clean and free from impurities such as grease, oil, gasket residues and other sealing products.
Degrease, clean and dry the parts before applying the product.
👉 Discover our complete selection of industrial cleaners and degreasers.
For maintenance and repair operations, remove old gasket residues using a dedicated remover, then clean the surfaces with an industrial degreaser.
If the gasketing product is applied at a temperature below 5 °C, pre-treat the surfaces with an activator.
👉 Discover our complete selection of primers and adhesive activators.
Contact us
Our technical experts are available to help you choose the most suitable flat gasketing product for your rigid or flexible joint faces.
Contact us now for:
a personalized recommendation
a fast quote
a product demonstration if needed
👉 Adezif optimizes your industrial assembly solutions. Contact us or call us directly.